Use of Polyjet technology in manufacture of personalised insoles
Identified Problem
While insoles are effective in alleviating the discomfort experienced by those with flat feet, there are several problems with regards to the manufacturing process of these insoles that can be improved on. Some of them are :
-
Fixed model is needed in advance
-
Multiple steps in production (molding) add to
-
Complexity
-
Cost
-
Skill set
-
Long wait for customers

Molding of insole
Solution Design
By 3D Printing these personalised insoles, the advantages we can expect are :
-
Greater production efficiency
-
Errors
-
Adjustments
-
Cost efficiency
-
Manpower
-
Material cost
-
Time efficiency
-
Maximum printing time of 2 days
What we need to do :
1) Testing of the materials ABS Plastic and rubber
- To ensure that the insole produced is neither too soft or too hard, ensuring comfort while being practical
2) Scanning of foot to serve as reference for the 3D model and eventually the 3D printed insole
- To ensure that the insole provides the correct fit for the user, minimizing the need for adjustments
3) Creating an inverse of the scanned foot
- To aid in the creation of the 3D model of the personalised insole


Inverse of simple model
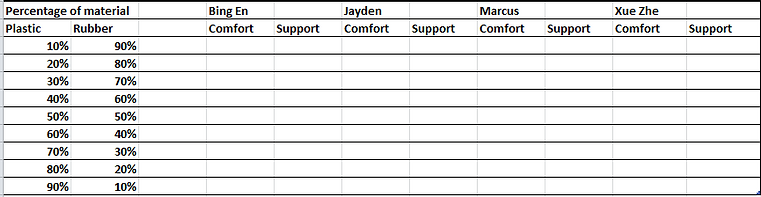
Table for recording of results
Problems encountered :
1) Scanning of foot
-
Lack of security key for scanning machine
-
Unable to scan foot
-
Time wastage, progress hindered
2) No immediate method of converting the file of the scanned foot into a 3D model
-
Tedious
-
Not entirely effective
Proudly created with Wix.com